Transport one of the largest belt conveyors in Japan
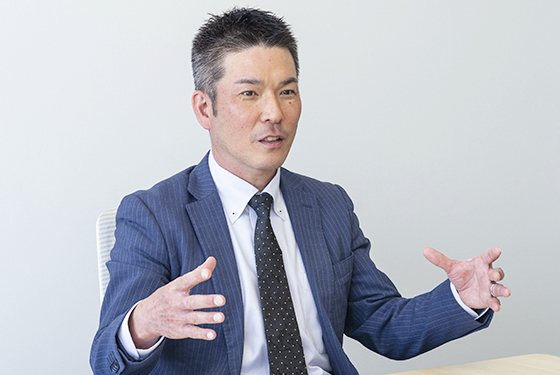
The project cargo transportation promotion team has been longing to take on the project for the transportation of transportation equipment, the Belt Conveyor System: hereinafter Belt Conveyor, which is known as one of the longest biomass transportations in Japan. We built trust with the client, a Japanese manufacturer, through various projects, starting with general air cargo. In the past, we took on a project for the transportation of belt conveyors and successfully completed the mission after earning the trust of our client. We were eager to take on the third project since we failed to take on the second one.
"We heard that our client experienced delivery delays and budget overruns on the second project with another company. Our client offered us the third project based on our successful experience on the first project and the trust we gained from the client. But I was unsure whether we could satisfy our client when we were notified to take on the third project, even though our client was satisfied with the result of our first project. Mr. Terada said.
This was because the belt conveyors were still being manufactured when we accepted the project. In addition, we were not fully informed of the exact dimensions of the large number of parts that would be shipped separately from overseas, or the exact delivery schedule.